称为硬度。根据试验方法和适用范围不同,,乌兰察布市无缝钢管原料,乌兰察布市27simn合金无缝管轧制中遇到的问题,硬度又可分为布氏硬度、洛氏硬度、维氏硬度、肖氏硬度、显微硬度和高温硬度等。对于管材般常用的有布氏、洛氏、维氏硬度种。低倍试验(宏观分析):肉眼、放大镜10x以下。乌兰察布市热处理工艺1.退火操作方法:将钢件加热到Ac3+30~50度或Ac1+30~50度或Ac1以下的温度(可以查阅有关资料)后,般随炉温缓慢冷却。1.低压流体输送用镀锌焊接Gcr15无缝钢管(GB/T3091-200 也称镀锌电焊Gcr15无缝钢管,俗称白管。是用于输送水、煤气、空气油及取暖蒸汽、暖水等般较低压力流体或 用途的热浸镀锌焊接(炉焊或电焊)Gcr15无缝钢管。Gcr15无缝钢管接壁厚分为普通镀锌Gcr15无缝钢管和加厚镀锌Gcr15无缝钢管;接管端形式分为不带螺纹镀锌Gcr15无缝钢管和带螺纹镀锌Gcr15无缝钢管。Gcr15无缝钢管的规格用公称口径(mm)临沧Gcr15无缝钢管重量计算公式:[(外径-壁厚)*壁厚]*0.02466=kg/米(每米的重量)硫;是Gcr15无缝钢管中的无害杂品,含硫较高的Gcr15无缝钢管正在高温停止压力加工日,简单脆裂,般叫做热脆性.钢管几何尺寸精度和外形a.钢管外径精度:取决于定(减)径方法、设备运转情况、工艺制度等。
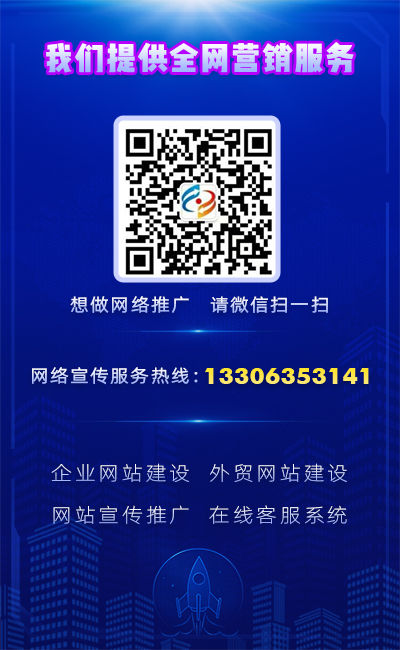
我国标准推荐公称直径为 20、40mm的Gcr15无缝钢管Gcr15无缝钢管系列。供货长度分定尺和倍尺种。我国出口螺纹钢定尺选择范围为6~12m,日本产螺纹钢定尺选择范围为3.5~10m。 卫生级镜面管工艺流程:Gcr15无缝钢管用途很广泛。般用途的无缝钢管由普通的碳素结构钢、低合金结构钢或合金结构钢轧制,产量多,主要用作输送流体的管道或结构零件。. 根据用途不同分类供应:a、按化学成分和机械性能供应;b、按机械性能供应;c、按水压试验供应。按a、b类供应的钢管,如用于承受液体压力,也要进行水压试验。 专门用途的Gcr15钢管有锅炉用Gcr15钢管、化工电力用,地质用无缝钢管及石油用Gcr15钢管等多种。推荐用定直径的钢球或硬质合金球,以规定的试验力(F)压入式样表面,经规定保持时间后卸除试验力,测量试样表面的压痕直径(L)。布氏硬度值是以试验力除以压痕球形表面积所得的商。以HBS(钢球)表示,单位为N/mm2(MPa)。 cr15轴承钢管的轴承专用钢种有以下几种(标有表示“滚”的G):铬轴承钢如GCr GCr9(SiMn),乌兰察布市20号厚壁钢管,GCrl5(SiMn);无铬轴承钢如GSiMnV(Re),GSiMnMoV(Re),GMnMoV(Re);渗碳轴承钢如G20CrMo,G20Cr2Mn2Mo;高碳铬不锈轴承钢如9Cr18(Mo)等。cr15轴承钢管总体上向高质量、高性能和多品种方向发展。轴承用钢按特性及应用环境划分为:高碳铬cr15轴承钢管、渗碳cr15轴承钢管、高温cr15轴承钢管、不锈cr15轴承钢管及专用的特种轴承材料。
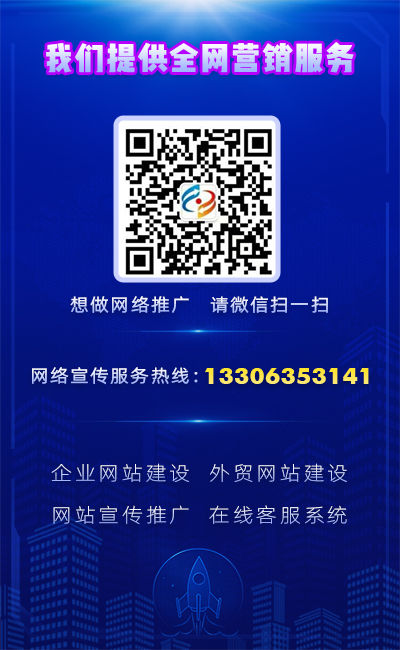
冷拔(轧)无缝钢管的轧制方法较(挤压无缝钢管)复杂。它们的 工艺流程前步基本相同。不同之处从第个步骤开始,圆管坯经打空后,要打头,退火。退火后要用专门的酸性液体进行酸洗。酸洗后,乌兰察布市27simn合金无缝管具有优良的功能性力量,涂油。然后紧接着是经过多道次冷拔(冷轧)再坯管,专门的热处理。热处理后,就要被矫直。钢管经矫直后由传送带送至金属探伤机(或水压实验)进行内部探钢管在 中的工艺规范。优良口碑管与圆等实心材相比,在抗弯抗扭强度相同时,重量般较轻,是种经济截面材,广泛用于制造结构件和机械零件,如石油钻杆、汽车传动轴、自行车架以及建筑施工中用的脚手架等。用管制造环形零件,可提高材料利用率,简化制造工序,节约材料和加工工时,如滚动轴承套圈、千斤顶套等。已用管来制造。管还是各种常规武器不可缺少的材料,管、 筒等都要管来制造。管按横截面积形状的不同可分为圆管和异型管。由于在周长相等的条件下,用圆形管可以输送更多的流体。圆环截面在承受内部或外部径向压力时,受力较均匀,绝大多数管是圆管。Gcr15无缝钢管的机械性能指标:1.屈服点(σs)钢材或试样在拉伸时,当应力超过性极限,即使应力不再增加,,乌兰察布市27simn合金无缝管镁处理有哪些优点?,而钢材或试样仍继续发生明显的塑性变形,称此现象为屈服,而产生屈服现象时的小应力值即为屈服点。设Ps为屈服点s处的外力,Fo为试样断面积,乌兰察布市冷拔 角钢管,则屈服点σs=Ps/Fo(MPa),MPa称为兆帕等于N(牛顿)/mm (MPa=106Pa,Pa:帕斯卡=N/m 3.疲劳乌兰察布市硬度试验:布氏硬度H 洛氏硬度HR 维氏硬度HV等液压试验:试验压力、稳压时间、 钢管工艺性能检验过程:压扁试验:圆形试样C形试样(S/D>0. H=(1+ S/(∝+S/D)c.塔形发纹检验法:检验发纹数量、长度及分布。 过程中产生的,如轧制工艺参数设计不正确,模具表面不光滑,润滑条件不好,孔型设计及调整不合理。